Regular Hair Canvas Interlining
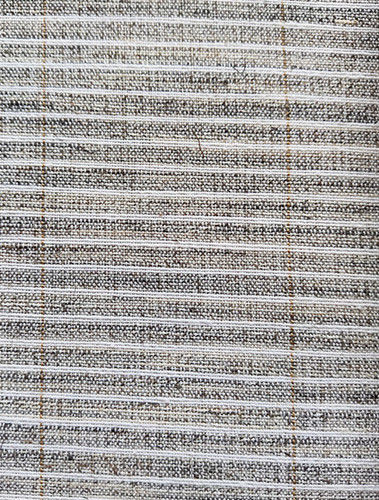
Hair canvas (Wool lining) is made of pure cotton yarn,goat hair,yak hair,human hair and viscose blended as weft.
Most hair canvas are black or grey
They are widely used in business suit, jacket, over coat with the excellent performance in elasticity, hardness and wrinkle resistance.
Hair canvas is ideal for high-grade clothing interlining, which can be used with fusible interlining in clothing.
Keep the chest, shoulder and sleeve parts in good shape, Make clothes are very stylish, plump, non-deformation, flat and neat surface, more comfortable in wearing.
The amount of adhesive can be variable depending on the pattern. The resin used can be selected from a group of polyurethanes, copolyamides, or other polymers.Pattern printing on a nonwoven base fabric can be achieved by either a flat or convex printing method. A concave printing pattern can be printed on a nonwoven interlining, whereas a flat pattern can be printed on a knitted interlining.Various physical properties of nonwoven interlinings are changed by pattern printing. This type of fabrication method is relatively simple. Moreover, this process has many benefits. For instance, it can be used to produce nonwoven base fabric with reinforced elasticity in both the width and longitudinal directions.In addition, the adhesive amount is adjustable, depending on the pattern. For example, the bonding weight can be 525 g/m2 or higher.In this type of fabrication, the substrate is the material onto which the thermoplastic resin is printed. The substrate can be the fabric or the composite material.Typical nonwovens are made by putting small fibers together in a sheet or web. These fabrics are typically made from polyester and other common fibers. They may be single-use or have long-lasting properties. They can mimic the texture of a woven fabric, but they can also mimic the strength and support of thick padding.The strength of the fabric depends on its fiber content.
There are many different fiber types, including polyester, polyethylene terephthalate, flax, and jute. Several special fibers are also used, including bi-component filaments and nanofiber. Moreover, the finish and diameter of the fibers have a large effect on the fabric's performance.The basis weight, fiber content and fabric fusing temperature. These three factors are important to ensure good results. To avoid improper attachment, choose the interlining according to these parameters. It is also important to consider the correct support and fusing conditions.The fabric surface properties determine the quality of the fused garment parts. This is particularly important before usage of garments.The tensile and elastic properties of shell fabric also affect compatibility with interlining. It is recommended that the difference in dimensional stability between the shell fabric and the interlining should be no more than two mm. If the difference is too large, the surface folding of stabilized garment parts could occur.Choosing the best interlining is a critical factor in the design process of garment production. The fabric's characteristics affect the look, feel and quality of the garment.
It is also a crucial factor in determining the cost and performance of the garment. Besides providing structural support, interlinings are used to prevent stretching and to improve the appearance of a finished garment.The performance of a fiber web depends on the amount of fiber in the fiber web, as well as the fiber orientation in the web. Various techniques can be applied to bond the fibers. Some of these processes are mechanical entanglement, thermal adherence, and a combination of both.Various studies have been carried out on nonwoven interlining. These studies highlight the advantages of printable interlining over traditional fusible interlinings. They are discussed, and are aimed at providing guidance for future research.Fiber webs are often used for interlining because of their versatility and low cost. Their performance is closely related to the fiber orientation in the web and the fabric weight. It is also important to consider the support and the fusing conditions.